Types of CNC machines play a crucial role in modern manufacturing, using automated precision to create parts with exact specifications. Whether it’s for automotive, aerospace, or medical industries, CNC machines are essential for producing high-quality, intricate components. These machines come in several varieties, each custom to specific tasks and needs:
- CNC Milling Machines: Best for shaping metal and other materials.
- CNC Lathe Machines: Ideal for making symmetrical parts.
- CNC Drilling Machines: Perfect for achieving precision holes.
- CNC Laser Cutting Machines: Great for intricate designs and cuts.
- CNC Grinding Machines: Used for precision finishing.
- CNC Plasma Cutting Machines: Designed for cutting conductive materials.
- CNC Waterjet Cutting Machines: Suited for versatile materials.
- Electric Discharge Machines (EDM): Works with conductive materials.
- 3D Printers: Used for prototyping through layer-by-layer creation.
- Multi-Axis CNC Machines: For complex parts with various axes configurations.
Precision machining is vital for companies that demand top-tier quality components for their industrial machinery. By selecting the right type of CNC machine, manufacturers can ensure their products meet exacting standards, enhancing the accuracy and longevity of their machinery. As industries advance, CNC technology continues to open up new precision possibilities, making it indispensable in the manufacturing world.
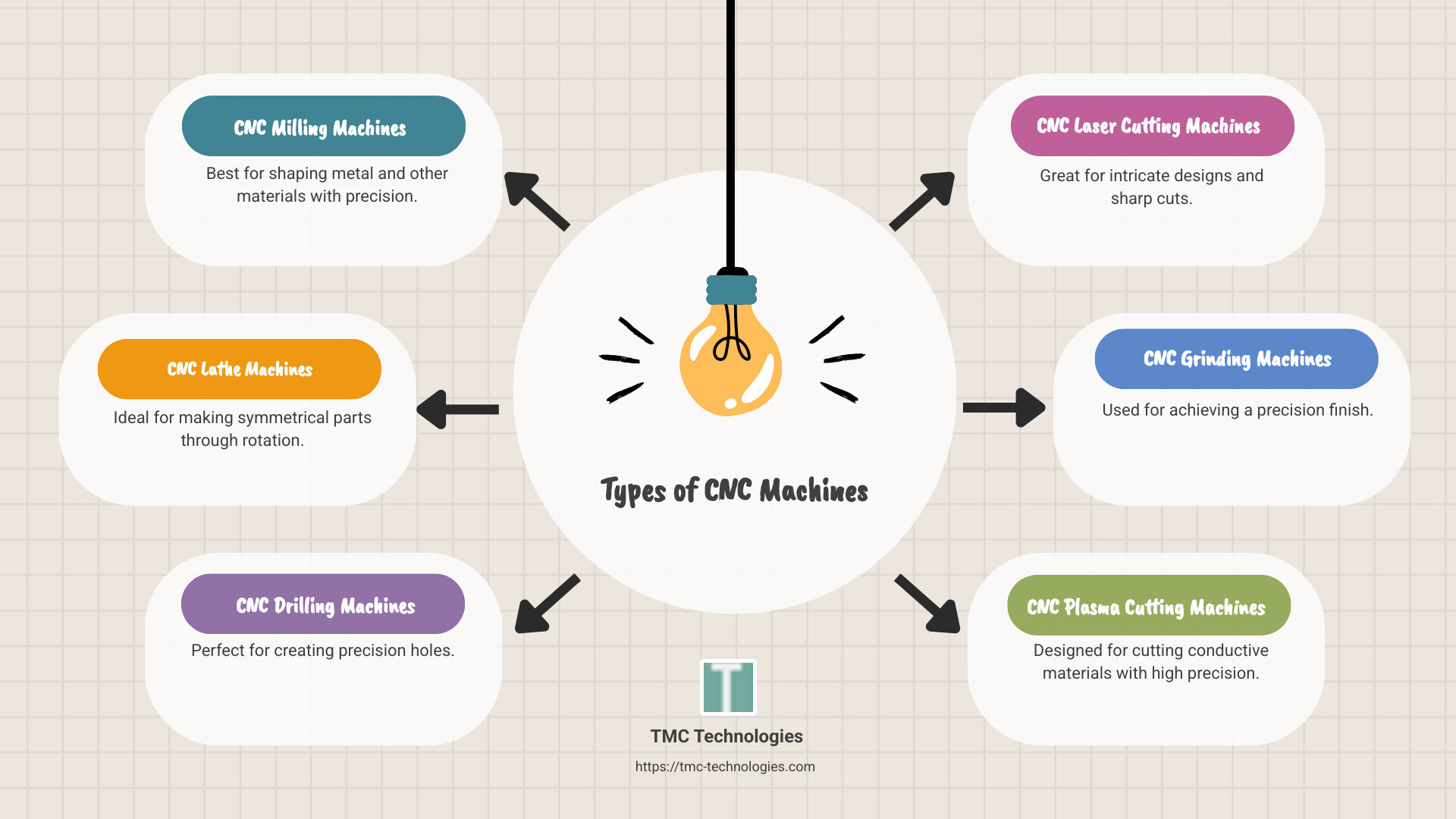
What is a CNC Machine?
A CNC machine, or Computer Numerical Control machine, is a marvel of modern manufacturing. It’s like having a robot that can create intricate parts with incredible precision. These machines are the backbone of industries like aerospace, automotive, and medical, where precision and accuracy are non-negotiable.
How CNC Machines Work
At the heart of a CNC machine is its ability to follow precise instructions. These instructions come from CAD/CAM software. CAD, or Computer-Aided Design, is where engineers create detailed models of the parts they need. CAM, or Computer-Aided Manufacturing, then takes these models and converts them into a language CNC machines understand: G-code.
G-code is like a recipe for the CNC machine. It tells the machine where to move, how fast to go, and what actions to take. This code ensures that every cut, drill, or grind is executed with pinpoint accuracy.
The Role of Precision
CNC machines excel in precision machining. They can produce parts with tolerances as tight as a few microns. This level of precision is crucial for industries where even the smallest error can lead to failure. For example, in the aerospace sector, precision machined parts are critical for safety and performance.
Efficiency and Consistency
One of the biggest advantages of CNC machines is their ability to work around the clock without losing consistency. They don’t tire, and they don’t make mistakes due to fatigue. This makes them ideal for producing large quantities of parts with the same high quality.
A Game-Changer in Manufacturing
CNC technology has transformed manufacturing. It allows for the production of complex parts that would be impossible to make by hand. This has opened up new possibilities in design and has enabled the creation of products with intricate details and superior performance.
As industries continue to push the boundaries of what’s possible, CNC machines will remain at the forefront, enabling precision and innovation in manufacturing.
Types of CNC Machines
CNC machines are the unsung heroes of modern manufacturing, offering a wide array of precision possibilities. Let’s explore some of the most common types of CNC machines and find how they contribute to various industries.
CNC Milling Machines
CNC milling machines are like the Swiss Army knives of the CNC world. They use rotary cutters to carve out precise shapes from solid materials. These machines are essential for tasks like face milling, shoulder milling, and drilling, making them a staple in industries such as automotive and aerospace. Equipped with multiple axes, they can handle complex geometries with ease.
CNC Lathe Machines
CNC lathes are masters at creating symmetrical parts. They rotate the workpiece while a stationary cutting tool shapes it. Ideal for producing cylindrical items like shafts and axles, CNC lathes offer best precision. The ability to create intricate designs with high accuracy makes them invaluable in manufacturing.
CNC Drilling Machines
When it comes to making precision holes, CNC drilling machines are the go-to choice. They use drill bits to create holes with exact specifications. These machines are versatile, working on materials ranging from metals to plastics, and are crucial in industries like electronics and automotive.
CNC Laser Cutting Machines
Laser cutting machines use focused laser beams to slice through materials with incredible precision. They are perfect for cutting intricate patterns and are widely used in the aerospace, automotive, and medical industries. However, they are limited to materials up to 2.75 inches thick.
CNC Grinding Machines
For a perfect finish, CNC grinding machines are the answer. They use a rotating wheel to smooth surfaces, providing a high-quality finish. These machines are essential for polishing and finishing tasks, especially in industries where precision is paramount.
CNC Plasma Cutting Machines
Plasma cutting machines use an electrical arc to cut through conductive materials. They offer high precision and are popular in metal fabrication and automotive repair. However, they produce a lot of heat, which can affect the surface finish.
CNC Waterjet Cutting Machines
Waterjet machines use high-pressure water to cut through a wide range of materials. They are incredibly versatile, able to shape everything from stone to metal. Their ability to cut without generating heat makes them ideal for materials sensitive to temperature changes.
Electric Discharge Machines (EDM)
EDMs use electrical discharges to shape materials. This non-contact process is perfect for creating complex parts that are difficult to machine with traditional methods. They are often used in mold-making and aerospace industries.
3D Printers
While not a traditional CNC machine, 3D printers deserve a mention. They build objects layer by layer, offering an innovative approach to manufacturing. Ideal for prototyping, they allow for quick iteration and design flexibility.
Multi-Axis CNC Machines
Multi-axis machines are the pinnacle of CNC technology. With four or more axes, they offer unparalleled flexibility and precision. These machines can produce complex parts with intricate details, making them indispensable in industries like aerospace and medical.
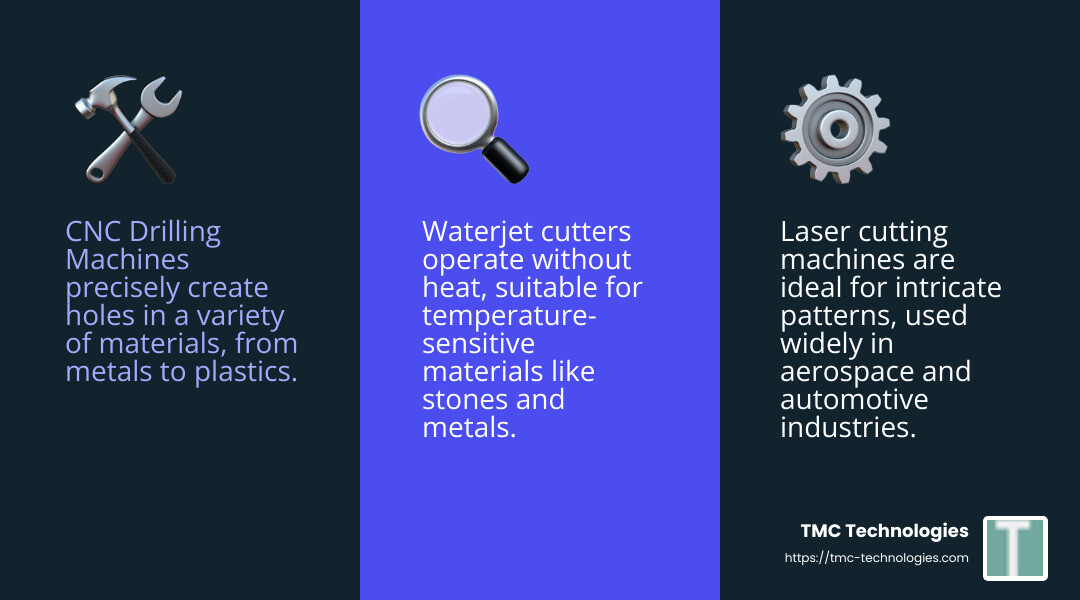
Understanding the types of CNC machines opens up a world of possibilities in precision machining. Each type brings unique capabilities, allowing manufacturers to produce high-quality, intricate designs with efficiency and accuracy.
CNC Milling Machines
CNC milling machines are the powerhouse of modern manufacturing, known for their versatility and precision. Imagine them as the sculptors of the industrial world, using rotary cutters to carefully carve out parts from solid blocks of material. They are indispensable in industries like automotive, aerospace, and medical, where precision and intricate designs are crucial.
Cutting Tools and Techniques
At the heart of CNC milling is the cutting tool. These tools come in various shapes and sizes, each designed for specific tasks like drilling, face milling, and slot milling. The choice of tool affects the quality and precision of the final product. For instance, end mills are commonly used for creating complex contours and profiles, while face mills are perfect for removing large amounts of material quickly.
Vertical vs. Horizontal Milling
CNC milling machines can be categorized into two main types based on the orientation of their spindles: vertical and horizontal.
-
Vertical Milling Machines have a spindle that is vertically oriented. This setup is ideal for tasks that require precision and detail, such as drilling and boring. They are highly versatile and widely used for creating precise machined parts.
-
Horizontal Milling Machines, on the other hand, have a horizontally oriented spindle. This configuration allows for more aggressive material removal and better chip evacuation, making them suitable for cutting large and heavy materials. They are often used for tasks that require extensive material removal.
Real-World Applications
CNC milling machines have revolutionized the way components are manufactured. For example, in the aerospace industry, they are used to create complex parts like turbine blades and engine components with high precision. In the automotive sector, they help in crafting intricate engine parts and chassis components.
A notable case is the use of CNC milling in the production of precision parts for the aerospace industry. These machines enable manufacturers to meet strict tolerance requirements, ensuring the safety and performance of aircraft.

In summary, CNC milling machines are essential tools in precision machining. Their ability to produce high-quality, intricate designs with efficiency makes them a cornerstone of modern manufacturing. As we continue to explore the different types of CNC machines, their unique capabilities open up a world of possibilities for creating precision machined parts.
CNC Lathe Machines
CNC lathe machines are like the artists of the CNC world, specializing in crafting perfectly symmetrical parts by rotating the workpiece. They are essential for producing cylindrical components with precision and speed.
The Basics of CNC Lathe Operation
In a CNC lathe, the workpiece spins around a central axis while a stationary cutting tool shapes it. This process is known as “turning.” By controlling the rotation speed and the tool’s position, CNC lathes can create precise cylindrical shapes. They can perform a variety of operations, including turning, facing, and threading.
Symmetrical Parts and Applications
CNC lathes are perfect for making parts that need to be symmetrical. Think of items like rods, shafts, and bushings. These machines are widely used in industries like automotive, aerospace, and medical, where precision and symmetry are critical.
For instance, in the automotive industry, CNC lathes produce engine components like crankshafts and camshafts. These parts must be perfectly balanced to ensure smooth engine operation. In the medical field, CNC lathes create components such as bone screws and implants, which require high precision for patient safety.
Advantages of CNC Lathes
- High Precision: CNC lathes offer best accuracy, making them ideal for parts that need tight tolerances.
- Efficiency: Once set up, they can produce parts quickly and consistently, reducing production time.
- Versatility: They can handle a variety of materials, including metals and plastics, making them adaptable to different manufacturing needs.
Real-World Example
A fascinating example of CNC lathe usage is in the aerospace industry. Companies use CNC lathes to produce critical components like turbine shafts, which require extreme precision and durability. The ability of CNC lathes to create these high-quality parts ensures the reliability and safety of aircraft.
In conclusion, CNC lathe machines are crucial for creating precision machined parts with symmetrical features. Their ability to deliver high-quality results efficiently makes them indispensable in modern manufacturing. As we dig further into CNC machines, their diverse capabilities continue to expand the possibilities for precision engineering.
CNC Drilling Machines
CNC drilling machines are the precision experts in creating holes with best accuracy and consistency. These machines play a crucial role in manufacturing, especially when precise holes are needed in various materials like metals and composites.
The Drilling Process
CNC drilling machines use drill bits to create holes in a stationary workpiece. The drill bit, held by a CNC-controlled spindle, rotates rapidly while moving downward into the material. This process ensures that each hole is drilled with exact precision, down to tolerances as small as 0.001 mm. The result is a series of perfectly aligned holes, essential for many industrial applications.
Precision Holes and Applications
The ability to drill precision holes is vital in numerous industries. In the automotive sector, for example, CNC drilling machines are used to create engine blocks and other components that require exact hole placement for bolts and fasteners. In the aerospace industry, these machines drill holes in aircraft components, ensuring the parts fit together perfectly for optimal performance.
CNC drilling machines are also indispensable in the production of electronic enclosures, where precise holes are needed for connectors and wiring. This ensures that the final product meets strict industry standards for quality and functionality.
Types of Drill Bits
CNC drilling machines accommodate a variety of drill bits, each suited for different tasks:
- Twist Drill Bits: Commonly used for general-purpose drilling.
- Step Drill Bits: Ideal for creating holes of varying diameters in a single pass.
- Annular Cutters: Used for drilling large holes with minimal material waste.
Advantages of CNC Drilling
- High Precision: Ensures exact hole placement and size, critical for components that must align perfectly.
- Flexibility: Capable of drilling through diverse materials, from metals to composites.
- Efficiency: Once programmed, CNC drills can produce large quantities of parts quickly and consistently.
Real-World Example
A notable example of CNC drilling in action is in the shipbuilding industry. Here, CNC drilling machines are used to create precise holes in large metal sheets, which are then assembled to form the hulls of ships. The accuracy of these machines ensures that each piece fits together seamlessly, contributing to the vessel’s structural integrity and safety.
In summary, CNC drilling machines are essential for creating precision machined parts with exact holes. Their ability to deliver high-quality results efficiently makes them a vital component of modern manufacturing. As we explore further into CNC machines, their diverse capabilities continue to push the boundaries of precision engineering.
CNC Laser Cutting Machines
CNC laser cutting machines are the maestros of precision cutting, using a focused laser beam to slice through materials with incredible accuracy. These machines are pivotal in industries where intricate designs and clean cuts are paramount, such as aerospace, automotive, and medical device manufacturing.
Types of Lasers
There are two main types of lasers used in CNC laser cutting machines:
-
CO2 Lasers: These are among the most common and are known for their ability to cut non-metal materials like wood, acrylic, and plastics. However, advancements in technology have enabled CO2 lasers to also cut through metals, though they excel in engraving and cutting organic materials.
-
Solid-State Lasers: These include fiber lasers and Nd:YAG lasers, which are highly effective at cutting metals. Solid-state lasers are renowned for their precision and speed, making them ideal for applications requiring detailed and fine cuts, such as in the production of electronic components and fine jewelry.
The Laser Cutting Process
CNC laser cutting machines operate by directing a high-powered laser beam through a series of mirrors or fiber optics. The beam is focused onto the material, heating it to the point of melting or vaporization. This process allows for clean and precise cuts, often with minimal waste.
The precision of laser cutting is measured in micrometers, ensuring that even the most intricate designs are executed flawlessly. This makes laser cutting an indispensable tool for producing precision machined parts.
Advantages of Laser Cutting
- High Precision: The focused laser beam allows for extremely accurate cuts, essential for complex and detailed designs.
- Versatility: Capable of cutting a wide range of materials, including metals, plastics, and even glass.
- Efficiency: Laser cutting is fast and can handle high-volume production runs with consistent quality.
Real-World Application
In the aerospace industry, CNC laser cutting machines are used to fabricate components that require exceptional precision and reliability. For example, laser cutting is employed to create lightweight metal parts that contribute to the overall efficiency and performance of aircraft. The precision of these machines ensures that each component meets stringent industry standards, enhancing the safety and functionality of the final product.
In conclusion, CNC laser cutting machines are key players in the field of precision machining. Their ability to deliver exact and efficient cuts makes them indispensable in modern manufacturing, driving innovation and quality across various industries. As we continue to explore the capabilities of CNC technology, the potential for even greater precision and efficiency remains vast.
CNC Grinding Machines
CNC grinding machines are at the forefront of precision machining, essential for achieving high-quality finishes on hard materials. These machines use a rotating grinding wheel to remove material from a workpiece, creating a precise and smooth surface. This capability is vital in industries such as automotive, aerospace, and medical technology, where accuracy and surface finish are non-negotiable.
The Grinding Process
The grinding process involves a rotating wheel that acts like a cutting tool, carefully removing tiny chips from the material’s surface. This method is not for shaping but for creating a precision finish. The grinding wheel’s rotation and the precise control of its movement allow for exceptional accuracy, producing parts that meet stringent specifications.
Applications of CNC Grinding
CNC grinding machines are used to create components like camshafts, ball bearings, and transmission shafts. These parts require a level of precision that only grinding can deliver. For example, in the automotive industry, these machines ensure that engine parts fit together perfectly, enhancing performance and longevity.
Key Features
- High Precision: CNC grinding machines can achieve tolerances as small as a few micrometers, ensuring that each part meets exact specifications.
- Surface Finish: The grinding process results in a smooth and polished surface, critical for reducing friction and wear in moving parts.
- Material Versatility: These machines can handle a wide range of hard materials, from metals to ceramics, making them indispensable in industries demanding high durability.
Leading Manufacturers
As of July 2024, some of the top CNC grinding machine manufacturers include JTEKT Toyoda Americas Corp., Delta Power Equipment Corporation, and Universal Grinding Corporation. These companies are renowned for their innovative approaches and high-quality machines that set industry standards.
Real-World Impact
In the aerospace industry, CNC grinding machines are crucial for producing parts that must withstand extreme conditions. For instance, turbine blades require precise grinding to ensure they operate efficiently and safely at high speeds. The precision and reliability of CNC grinding machines make them indispensable tools in the production of these critical components.
In summary, CNC grinding machines play a pivotal role in precision machining. Their ability to deliver exact finishes and handle hard materials makes them essential in modern manufacturing, contributing to the production of high-quality, reliable parts across various industries. As we dig deeper into CNC machining capabilities, the potential for even greater precision and innovation continues to grow.
CNC Plasma Cutting Machines
CNC plasma cutting machines are a powerhouse in the field of precision machining, renowned for their ability to cut through electrically conductive materials with high precision and speed. These machines are indispensable in industries like automotive and metal fabrication, where efficiency and accuracy are paramount.
How Plasma Cutting Works
Plasma cutting employs a high-speed jet of hot plasma to cut through materials. This plasma is created by electrically heating a gas, which then ionizes and becomes capable of conducting electricity. The ionized gas, or plasma, is forced through a nozzle, creating a precise and high-temperature stream capable of slicing through metals like steel and aluminum.
Advantages of Plasma Cutting
- High Precision: Plasma cutters can achieve clean and precise cuts, making them ideal for intricate designs and complex shapes.
- Speed: The cutting speed of plasma machines is significantly faster than traditional methods, boosting productivity.
- Versatility: These machines can handle various conductive materials, including steel, stainless steel, and aluminum.
Limitations
While plasma cutting offers numerous advantages, it does have some limitations. It is best suited for conductive materials and may not be ideal for non-conductive materials like plastics or composites. Additionally, the high temperatures involved can lead to a heat-affected zone around the cut area, which might require additional finishing.
Real-World Applications
Plasma cutting finds applications across multiple industries. In the automotive sector, it is used for cutting body panels and frames. In fabrication shops, plasma cutters are employed to create structural supports and brackets with precision. The ability to cut irregular and curved shapes makes them valuable in custom manufacturing and repair work.
Leading Brands
Top brands like ESAB, Cruxweld, and Lincoln dominate the CNC plasma cutting market, offering machines that range from small-scale models priced at around $12,000 to larger, industrial-sized machines that can exceed $50,000. These brands are known for their reliability and innovation, ensuring that businesses can meet their precise cutting needs efficiently.
In summary, CNC plasma cutting machines are a vital tool in modern manufacturing, providing the precision and speed necessary for high-quality production. Their ability to handle a variety of conductive materials makes them a versatile choice for industries that demand accuracy and efficiency. As technology advances, the capabilities of these machines continue to expand, offering even greater possibilities for precision machining.
CNC Waterjet Cutting Machines
CNC waterjet cutting machines are a marvel of modern engineering, using high-pressure water jets to slice through a wide range of materials with incredible precision. Unlike other cutting methods, waterjet cutting is unique because it doesn’t rely on heat, making it a go-to choice for materials that are sensitive to temperature changes.
How Waterjet Cutting Works
This process involves a high-pressure stream of water, often mixed with an abrasive material like garnet, to improve cutting power. The water is pressurized up to 60,000 psi and forced through a small nozzle to create a highly focused and powerful jet. This jet can cut through materials ranging from soft rubber to hard metals with remarkable accuracy.
Advantages of Waterjet Cutting
- Versatility: Waterjet machines can cut virtually any material, including metals, stone, glass, and composites. This versatility makes them ideal for industries like aerospace, automotive, and construction.
- Cold Cutting Process: Because waterjets cut without heat, there is no heat-affected zone. This means the material’s intrinsic properties remain unchanged, preserving its structural integrity.
- Precision: With the ability to cut complex shapes and intricate patterns, waterjet machines offer precision that is hard to match with other cutting technologies.
Limitations
Despite their many advantages, CNC waterjet cutting machines do have some limitations. The cutting speed is generally slower compared to laser or plasma cutters, especially for thicker materials. Additionally, the initial setup and operational costs can be higher due to the need for high-pressure pumps and maintenance of abrasive materials.
Real-World Applications
Waterjet cutting is widely used in the aerospace industry for cutting parts that require high precision and no thermal distortion. In the automotive sector, it is employed for creating intricate parts and prototypes. The construction industry benefits from waterjet cutting for shaping stone and tiles with precision.
Leading Brands
Prominent brands like Flow International, OMAX Corporation, and KMT Waterjet lead the market with their innovative waterjet cutting solutions. These companies offer a range of models suitable for different scales of production, from small workshops to large industrial operations.
CNC waterjet cutting machines provide a versatile and precise solution for cutting a wide array of materials. Their ability to maintain material integrity while delivering intricate cuts makes them indispensable in industries that demand high-quality and precise machining. As technology progresses, waterjet cutting continues to evolve, offering even more possibilities for precision manufacturing.
Electric Discharge Machines (EDM)
Electric Discharge Machines (EDM) are a fascinating type of CNC technology that harnesses the power of electrical discharges to shape materials. Often referred to as spark CNC machines, these devices excel in working with electrically conductive materials such as steel, brass, and titanium.
How EDM Works
EDM operates on a simple yet powerful principle: eroding material through a series of controlled electrical discharges. The process involves an electrode and the workpiece, which are submerged in a dielectric fluid. When a voltage is applied, sparks fly between the electrode and the material, vaporizing tiny bits of the workpiece. This method allows for incredibly precise material removal without any direct contact between the tool and the material.
Advantages of EDM
- Complex Shapes: EDM can create intricate and complex shapes that are difficult to achieve with traditional machining methods. This makes it ideal for producing molds, dies, and detailed parts.
- No Mechanical Stress: Since the process involves no physical contact, there is no mechanical stress on the workpiece. This is particularly beneficial for delicate or thin materials.
- Material Hardness: EDM is unaffected by the hardness of the material, allowing it to machine tough alloys and hardened steels with ease.
Limitations
Despite its many benefits, EDM does have some drawbacks. It is generally slower than other cutting methods like plasma or laser cutting, making it less suitable for high-speed production. Additionally, EDM can only work with electrically conductive materials, which limits its application scope.
Real-World Applications
EDM is widely used in industries that require high precision and complex geometries. In the medical field, it is employed to create intricate components for implants and surgical instruments. The aerospace industry uses EDM for crafting components that require tight tolerances and unique shapes. Additionally, EDM is essential in the tool and die industry for producing molds and dies with complex features.
Leading Brands
Some of the top brands in the EDM market include Makino, FANUC, and Accutex. These companies offer a range of EDM machines, from small, cost-effective models to advanced systems designed for high-precision applications.
In summary, Electric Discharge Machines (EDM) are a vital tool in precision machining. Their ability to produce complex shapes without mechanical stress makes them indispensable in industries that demand accuracy and detail. As technology advances, EDM continues to push the boundaries of what is possible in precision manufacturing.
3D Printers
In CNC machine types, 3D printers stand out for their unique approach to creating parts. Unlike traditional subtractive methods, 3D printers use additive manufacturing to build objects layer-by-layer. This innovative process opens up new possibilities for prototyping and production in various industries.
How 3D Printing Works
3D printing begins with a digital design, often created using CAD software. The design is sliced into thin layers, and the printer builds the object by adding material layer-by-layer. This method allows for complex geometries that would be challenging or impossible to achieve with subtractive manufacturing.
Advantages of 3D Printing
- Design Freedom: 3D printers can create intricate designs and complex structures without the constraints of traditional machining. This makes them ideal for crafting custom parts and prototypes.
- Reduced Waste: Additive manufacturing uses only the material needed for the part, significantly reducing waste compared to traditional methods.
- Rapid Prototyping: 3D printers can quickly produce prototypes, allowing for faster design iterations and development cycles.
Limitations
While 3D printing offers many benefits, it also has limitations. It is generally slower than other manufacturing methods, making it less suitable for high-volume production. Additionally, 3D printing is often limited to specific materials, such as plastics and a few metals, which may not meet all application requirements.
Real-World Applications
3D printing is revolutionizing industries by enabling rapid prototyping and production of complex parts. In the aerospace sector, it is used to create lightweight components that improve fuel efficiency. The medical industry leverages 3D printing to produce custom implants and surgical guides custom to individual patients. In consumer electronics, 3D printers help design and test new product enclosures and components.
Leading Brands
Some of the top brands in the 3D printing market include FlashForge, 3D Systems, Markforged, and Raise 3D. These companies offer a range of printers, from desktop models for small-scale projects to industrial machines capable of producing large, intricate parts.
3D printers are changing how we approach manufacturing and design. Their ability to produce complex parts with minimal waste makes them a valuable tool in the pursuit of innovation and efficiency. As technology continues to advance, 3D printing will undoubtedly play a pivotal role in shaping the future of manufacturing.
Multi-Axis CNC Machines
When it comes to CNC precision machining, multi-axis machines are the pinnacle of technology and innovation. These machines offer best capabilities for creating complex parts with high precision and efficiency. Let’s explore multi-axis CNC machines, particularly focusing on the 5-axis and 12-axis variants.
Understanding Multi-Axis Machining
Traditional CNC machines operate on three axes: X, Y, and Z, which limits the complexity of parts they can create. Multi-axis CNC machines add additional axes, allowing the cutting tool to approach the workpiece from multiple angles. This flexibility is crucial for crafting intricate designs and achieving tight tolerances.
5-Axis CNC Machines
5-axis CNC machines are a game-changer in the manufacturing industry. They add two rotational axes, usually referred to as A and B, to the standard three linear axes. This configuration enables the tool to move around the workpiece in a way that allows for the machining of complex geometries in a single setup.
- Benefits of 5-Axis Machining:
- Complex Geometries: Ideal for parts with intricate shapes, such as turbine blades and medical implants.
- Reduced Setups: Multi-sided machining in one setup reduces time and potential errors.
- Improved Surface Finish: The ability to use shorter tools reduces vibration and improves surface quality.
12-Axis CNC Machines
Taking it to the next level, 12-axis CNC machines are among the most advanced in the industry. These machines feature two cutting heads, each capable of moving along six axes (X, Y, Z, A, B, and C). This setup dramatically increases both precision and production speed.
- Applications of 12-Axis Machining:
- High-Precision Parts: Used in industries requiring extreme accuracy, such as aerospace and military.
- Simultaneous Machining: Two heads working in tandem can double the productivity, making them ideal for mass production of complex parts.
Real-World Applications
In the aerospace industry, multi-axis CNC machines are essential for crafting lightweight, high-strength components. The medical field benefits from these machines for producing custom implants and surgical tools. Even in the automotive sector, multi-axis machining is used for engine components and intricate interior parts.
Case Study: TMC Technologies
At TMC Technologies, we harness the power of multi-axis CNC machines to deliver precision machined parts to our clients. Our facilities in Carroll, IA, are equipped with the latest technology, allowing us to meet the demanding requirements of industries such as aerospace, medical, and automotive. By leveraging multi-axis capabilities, we ensure our clients receive high-quality, intricate designs with exceptional accuracy.
In conclusion, multi-axis CNC machines are revolutionizing the way we approach manufacturing. Their ability to produce complex parts with precision and efficiency makes them an invaluable asset in modern production environments. As technology continues to advance, the possibilities for multi-axis machining will only expand, paving the way for even more innovative solutions.
CNC Machine Types by Number of Axes
CNC machines come in various configurations, primarily distinguished by the number of axes they operate on. Each type offers unique capabilities, making them suitable for different manufacturing needs. Let’s explore the types of CNC machines based on their axes.
2-Axis CNC Machines
2-axis CNC machines are the most basic in the lineup. They operate along the X and Y axes, moving horizontally and vertically. These machines are ideal for simple tasks like drilling holes or cutting straight lines. While limited in complexity, they are cost-effective solutions for straightforward manufacturing needs.
- Applications:
- Basic Drilling: Creating holes in boards and panels.
- Straight Cuts: Ideal for projects requiring linear cuts without depth variation.
3-Axis CNC Machines
The 3-axis CNC machines add a Z-axis to the mix, allowing for depth control. This enables more complex operations, such as milling and engraving, on stationary workpieces. These machines are the workhorses of many industries, providing a balance of complexity and affordability.
- Applications:
- Milling: Suitable for creating 2.5D shapes and features.
- Engraving: Engraving intricate designs on flat surfaces.
4-Axis CNC Machines
4-axis CNC machines introduce an A-axis, which allows rotation around the X-axis. This additional axis enables the machining of cylindrical objects and more complex geometries. They are particularly useful for tasks like engraving on curved surfaces.
- Applications:
- Rotational Engraving: Ideal for cylindrical objects like pipes and rods.
- Arc Cutting: Allows for creating arcs and circular features.
5-Axis CNC Machines
With 5-axis CNC machines, two more rotational axes (A and B) are added, enabling the tool to approach the workpiece from virtually any direction. This flexibility is crucial for crafting intricate parts with minimal setups.
- Applications:
- Complex Geometries: Essential for aerospace components and medical implants.
- Reduced Setup Time: Multi-sided machining in one setup improves efficiency.
9-Axis CNC Machines
A 9-axis CNC machine combines a 5-axis milling and a 4-axis lathe machine. This setup allows for simultaneous internal and external feature machining, making it ideal for complex parts that require both milling and turning.
- Applications:
- Medical Instruments: Perfect for producing dental implants and surgical tools.
- Aerospace Components: Suitable for intricate parts with both internal and external features.
12-Axis CNC Machines
The pinnacle of CNC technology, 12-axis CNC machines feature two cutting heads, each capable of moving along six axes. This setup maximizes precision and doubles productivity, ideal for high-volume production of complex parts.
- Applications:
- High-Precision Manufacturing: Used in aerospace and military industries.
- Simultaneous Machining: Two heads working together significantly increase output.
In CNC precision machining, the number of axes a machine operates on directly impacts its capabilities and applications. Whether it’s the simplicity of a 2-axis or the complexity of a 12-axis machine, each type serves a specific purpose in the manufacturing landscape. As we continue to innovate, these machines will undoubtedly play a pivotal role in shaping the future of precision manufacturing.
CNC Precision Machining
CNC precision machining is all about creating parts with exceptional accuracy, efficiency, and detail. This process is vital for industries needing high-quality components, such as aerospace, medical, and electronics.
Precision
Precision is the cornerstone of CNC machining. It ensures that every part produced meets strict tolerances. For example, CNC machines can achieve tolerances as tight as +/- 0.001 inches. This level of precision is essential for parts that must fit together perfectly, like the intricate components used in aerospace or medical devices. In these fields, even minor deviations can lead to failures, making precision non-negotiable.
Accuracy
Accuracy in CNC machining means hitting the exact dimensions every time. This is achieved through advanced software and high-quality tooling. CNC machines use sophisticated software to interpret CAD designs and generate precise cutting paths. As a result, each cut is made exactly as planned. High-quality tools, which are sharp and durable, further improve accuracy by reducing errors during the machining process.
Efficiency
Efficiency is another key benefit of CNC precision machining. Automated control systems minimize human error and ensure consistent quality across large production runs. This is particularly important for industries requiring mass production of identical parts. Machines like 5-axis CNC mills can create complex geometries and intricate designs that would be impossible with manual machining, all while reducing setup times and increasing throughput.
By leveraging the power of CNC precision machining, companies like TMC Technologies can deliver high-quality, intricate designs that meet the exacting standards of their clients. This capability not only improves the quality of the products but also streamlines the manufacturing process, making it more cost-effective and reliable.
As we dig deeper into precision machined parts, we’ll see how these principles come to life in various industries and applications.
Precision Machined Parts
Precision machined parts are the backbone of modern manufacturing, providing the high-quality and intricate designs required in industries such as aerospace, medical, and electronics. These parts must meet exacting standards, and TMC Technologies excels in delivering these components with best precision.
High-Quality Standards
At TMC Technologies, quality is not just a goal—it’s a guarantee. By using state-of-the-art CNC machines, the company ensures that every part produced meets stringent specifications. This commitment to quality is critical in industries where even the smallest error can lead to significant issues. For instance, in the medical field, a tiny flaw in a machined part could compromise the safety of an entire device.
Intricate Designs
The capability to produce intricate designs is one of the standout features of CNC machining. With advanced software and multi-axis machines, TMC Technologies can create components with complex geometries that would be impossible to achieve with traditional methods. This ability is particularly valuable in the aerospace industry, where parts often have complex shapes and must withstand extreme conditions.
TMC Technologies’ Expertise
Located in Carroll, IA, USA, TMC Technologies is a leader in CNC machining, known for its expertise and reliability. The company uses cutting-edge machinery to fulfill the diverse needs of its clients, ensuring each part is crafted to perfection. Their advanced CNC mills and lathes can handle a wide range of materials, delivering parts with exceptional precision and consistency.
Real-World Applications
Precision machined parts play a crucial role across various sectors. In aerospace, they contribute to the safety and efficiency of aircraft. In electronics, they are essential for creating components that power devices we use daily. TMC Technologies’ ability to produce these parts with high precision and intricate designs makes them a trusted partner for companies seeking excellence in manufacturing.
In the next section, we’ll explore frequently asked questions about CNC machines, diving into the different types and their specific purposes.
Frequently Asked Questions about CNC Machines
What are the 5 common types of CNC machines?
The world of CNC machines is vast, but five types stand out for their widespread use and versatility:
-
CNC Milling Machines: These machines use rotating cutting tools to remove material from a workpiece. They are ideal for creating complex parts with high precision, making them essential in industries that demand intricate designs.
-
CNC Lathes: Known for their ability to produce symmetrical parts, CNC lathes rotate the workpiece while a stationary cutting tool shapes it. This process is perfect for crafting cylindrical components found in automotive and aerospace applications.
-
CNC Drilling Machines: As the name suggests, these machines are used to drill precise holes into materials. They are crucial in manufacturing processes that require accuracy and consistency in hole placement and size.
-
CNC Plasma Cutters: Utilizing a plasma torch, these machines cut through conductive materials like steel and aluminum with high precision. Their ability to handle thick materials makes them popular in heavy industries.
-
CNC Laser Cutting Machines: These machines use lasers to cut materials with extreme accuracy. They are especially useful for cutting complex shapes in sheet metal, plastics, and other thin materials.
Are all CNC machines the same?
Not at all. CNC machines come in various types, each designed for specific purposes. While they all operate using G and M codes—the programming language that controls their movements—their applications can differ significantly. For instance, a CNC mill is built for milling operations, while a CNC lathe is best for turning operations. The choice of machine depends on the material, the complexity of the part, and the required precision.
What is a 12-axis CNC machine?
A 12-axis CNC machine is a marvel of modern engineering, offering unparalleled productivity and versatility. Unlike traditional machines, it features two heads that can move along multiple axes—X, Y, Z, A, B, and C—simultaneously. This allows for complex parts to be machined from multiple angles without the need for repositioning. The result is faster production times and the ability to create intricate components with high precision, making it an invaluable tool in industries that demand cutting-edge technology.
In summary, the diversity of CNC machines allows for a wide range of applications, each custom to meet specific manufacturing needs. Whether it’s the precision of a milling machine or the versatility of a 12-axis system, CNC technology continues to revolutionize manufacturing.
Conclusion
At TMC Technologies, we understand that precision is not just a requirement—it’s an expectation. Our commitment to excellence in CNC machining ensures that we deliver high-quality precision parts that meet the exacting standards of various industries.
CNC machining has revolutionized the manufacturing world, allowing for the creation of intricate designs with unparalleled accuracy. From aerospace to medical devices, our CNC components are crafted to withstand the rigors of their intended applications. This level of detail is achieved through our investment in advanced technology and skilled professionals who are dedicated to delivering the best possible results.
Our facility, located in Carroll, Iowa, is equipped with state-of-the-art machinery, including multi-axis CNC machines that allow us to handle complex projects with ease. This capability is crucial for industries that demand high precision and efficiency in their components. Our 9-axis CNC machines exemplify our commitment to staying at the forefront of technological advancements, providing our clients with the precision and versatility they need.
We pride ourselves on our ability to offer custom solutions custom to our clients’ unique requirements. Whether you need a prototype or full-scale production, we are equipped to handle projects of any size and complexity. Our expertise in tool design and fabrication ensures that every part we produce is of the highest quality, meeting the specific needs of your project.
In conclusion, TMC Technologies is more than just a CNC machine shop. We are a partner in your success, committed to delivering precision, quality, and innovation in every component we produce. As the future of CNC machining evolves, we remain dedicated to pushing the boundaries of what’s possible, ensuring that our clients receive the best products and services available.